by Sandra Vogt, Emtec Electronic GmbH
Paper production is a complex and dynamic process with countless variables and adjustments in the production plant. By increasing the level of automation and monitoring of the plant, it is possible to increase the efficiency of the entire process. Of all the parameters, monitoring the slurry charge – colloidal charge and fibre zeta potential – and the entire wet-end is extremely important
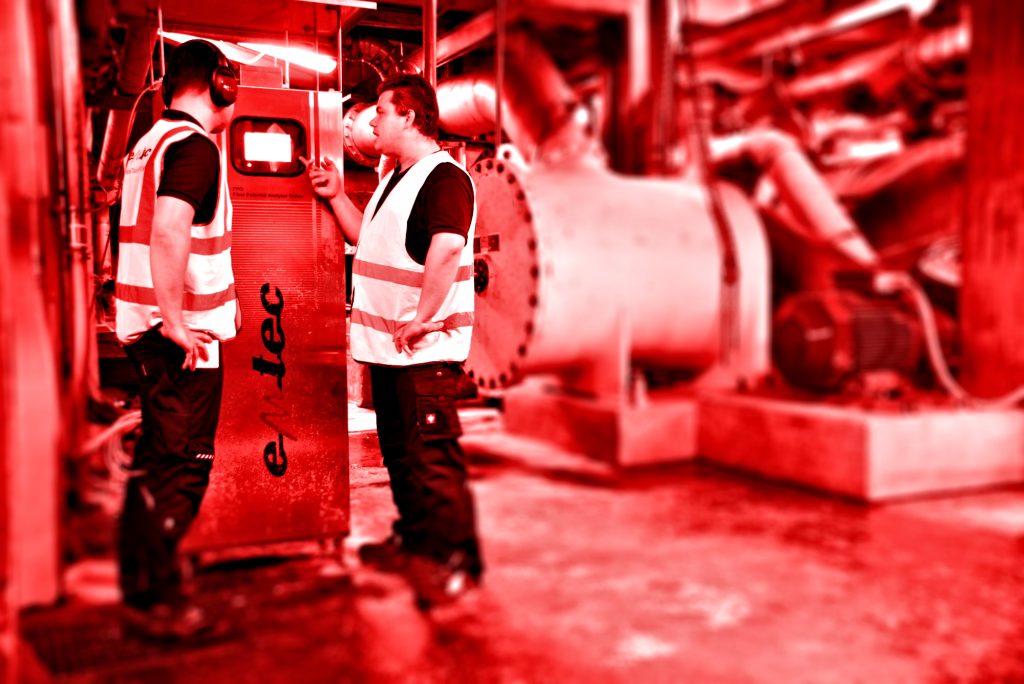
Improperly managed charging situations can lead to losses in terms of product quality, process fluctuations and increased consumption of auxiliaries. Constant control is particularly useful when using different chemical additives that require precise operating conditions to ensure consistent results. By constantly knowing the system’s charge, it is possible to optimize the dosages of the entire wet-end and keep the process under constant control.
Useful analytical tools to retrieve this information are -for example- the CAS touch! Charge Analysing System and the FPA touch! Fibre Potential Analyzer. These devices are already used in the laboratory and are well known within the paper industry. In addition to the established use of this technique, both devices offer a particular immediacy of use and effectiveness.
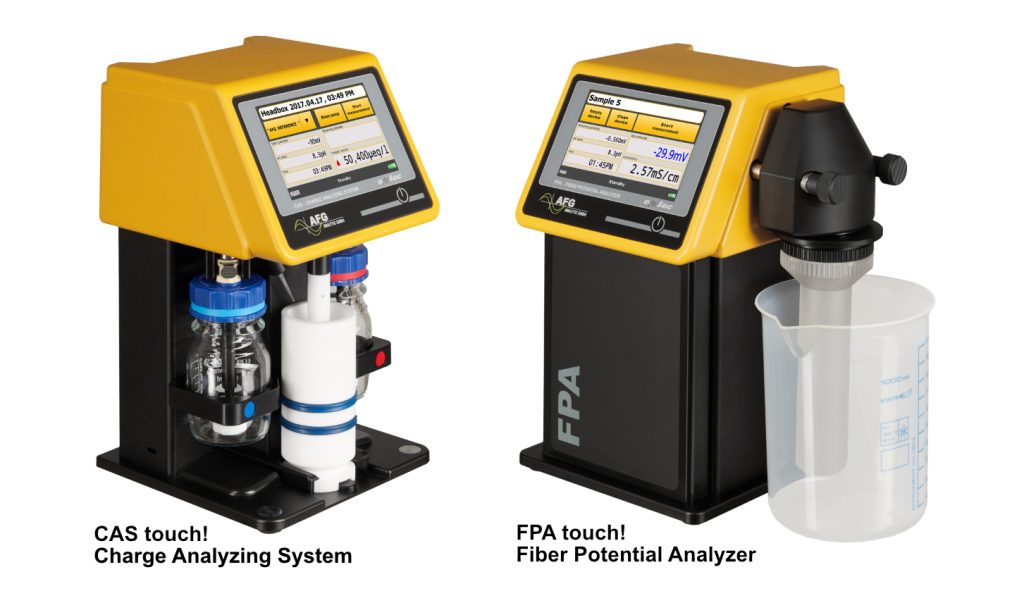
Auxiliary technicians in particular appreciate their portability and the fact that they are ready to use without any installation. However, with the increasing role that automation and digitization are taking on in paper production, as well as in other industries, automatic measurements that allow continuous and timely process value readings have become increasingly important in order to achieve sustainability and production efficiency goals. At the same time, such on-line measurements offer several advantages, first and foremost the availability of results in real time, without the need for manual sampling, which allows for timely corrective action, which can also be limited in scope and ensures that product quality is maintained within the desired specifications. Furthermore, these measured data, as well as being sent to DCS, can be made available on the cloud, both for distributed quality control purposes and for functional and maintenance checks that can also be carried out remotely, without the need to be on-site.
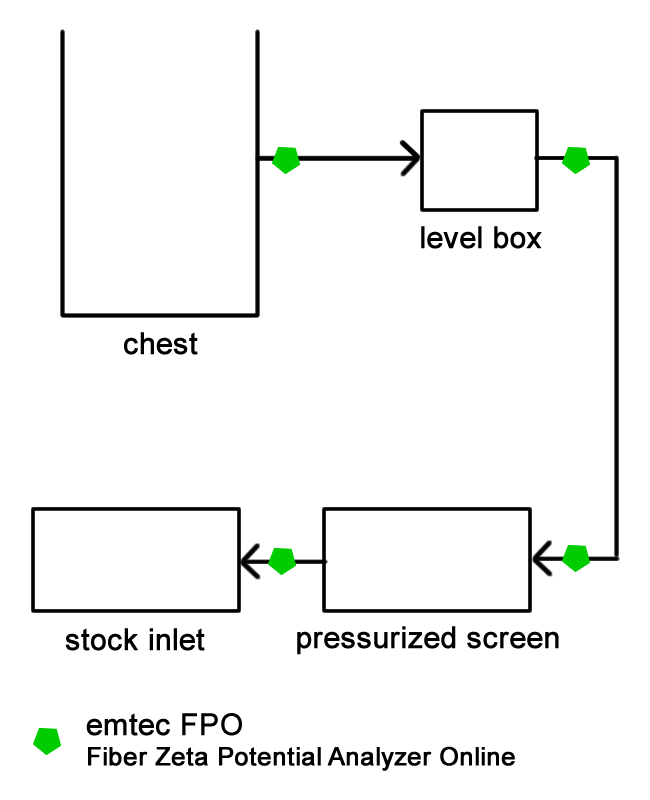
One such line device is the FPO Fiber Potential Analyzer Online from Emtec. The device measures fibre zeta potential directly and automatically on machine circuits. It samples, measures and cleans, requires minimal maintenance and can be installed at various points in the plant, even two sampling points in sequence, before and after the addition of an additive – for example. The FPO can make up to six measurements per hour, depending on process requirements. The measurement principle of the line instrument is the same as that of the laboratory instrument; both determine the zeta potential of fibers suspended in the wet-end circuits, a potential that is calculated using the Helmholtz- Smoluchowski equation.
The data, including fiber zeta potential, streaming potential, conductivity, pH and temperature, are transferred to the process control (e.g. DCS) where changes resulting from the chemical situation in the line can be immediately observed. This makes the device extremely useful for process optimization and control as well as product quality improvement.
To optimize the use of chemical additives in the process while maintaining consistent quality, the FPO Fiber Potential Analyzer Online helps determine the appropriate amount of additives for anionic residues, sizing, dry and wet strength, optical brighteners, softeners and dyes. In addition, knowledge of the zeta potential helps in a number of situations: it is crucial for optimizing the retention of fines, fillers, dyes and resins; for optimal sizing, neutralizing anionic residues and handling numerous situations such as inserting coated foils, operations in the water circuit, and many other situations where the device provides the necessary data to stabilize the process
One case where the device shows its advantages is a paper mill that alternately produces different types of paper.
Both types of base paper have to achieve very different product specifications.
Changing the type of production from one product to another, e.g. from toilet paper to kitchen paper, requires both a change in the type of pulp (e.g. fiber type) but also the type of additives. Changing additives requires skillful dosing so that the addition is effective. In order to do this, it is necessary to know the zeta potential of the fiber in the pulp, so as to know the receptive capacity to additives, which would otherwise be wasted by remaining in the water circuit and causing problems of runnability and water circuit disturbances, very difficult to solve blindly, without knowing the charge values in the circuit.
Emtec’s FPO, measures zeta potential directly in-line and provides real-time data that helps to achieve the required targets in the shortest possible time as direct measurement of fiber charge allows precise detection of satisfactory additive quality, predicting well in advance, and therefore less waste, mechanical lab results that remain necessary, but only confirmatory and no longer predictive. This shortens the control cycle, shortens time, saves money in additives and energy and improves productivity.
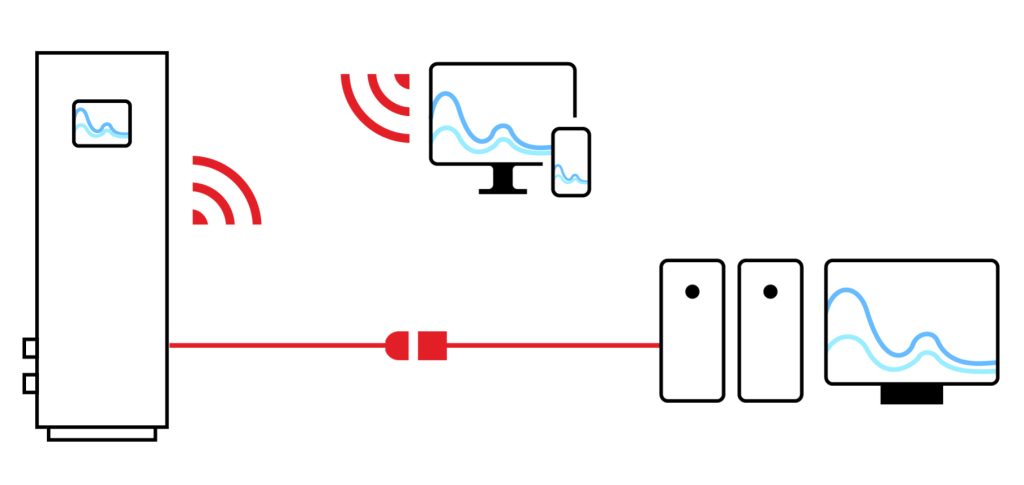
The FPO is an inline system that produces real-time data, helping the industry towards digitization and automation of the paper production process. The device operates in accordance with Industry 4.0 specifications, working fully automatically, reliably and accurately, with minimal maintenance requirements. The data is made available both to DCS and to the cloud from which it can be consulted both centrally at group level for statistical and corporate purposes, and for troubleshooting, allowing technical intervention or advice from the parent company in a very short time, even during periods of difficult or limited mobility. The system also has possible automatisms that can be configured for automatic actions in reaction to events (e.g. automatic additions in case of out-of-specification),
The European Commission has already indicated that Industry 4.0 must lead to digitally interconnected companies, with data exchange in order to optimise processes and logistics efficiency, rethinking their role with respect to society and the environment. In this perspective, the concept has been extended in Industry 5.0, which focuses on industries more at the service of the planet and mankind, with explicit reference to “energy cost” and “economic growth”. Following this indication, several European countries have introduced programmes to economically support the renovation of industrial processes, especially energy-consuming ones, by incentivizing energy saving, recycling, and the reduction of resource consumption. Using FPO goes fully in this direction. offering process optimization, which leads to maximizing productivity, reducing waste and energy.